羅茨水環(huán)機組:塑膠廠“全年無休”的硬核生產(chǎn)力引擎
在塑膠加工行業(yè),設備宕機是懸在生產(chǎn)線上方的“達摩克利斯之劍”。傳統(tǒng)真空泵因故障頻發(fā)、能耗失控,常讓企業(yè)陷入“停機搶修—訂單積壓—利潤縮水”的惡性循環(huán)。而羅茨水環(huán)真空機組的出現(xiàn),正以“全年無休”的穩(wěn)定性、“三防一體”的硬核性能,重塑塑膠廠的生產(chǎn)邏輯。工人從“救火隊員”變身“巡檢員”,老板直呼“省下的錢夠換輛特斯拉”——這場由真空系統(tǒng)引發(fā)的效率革命,正在顛覆行業(yè)認知。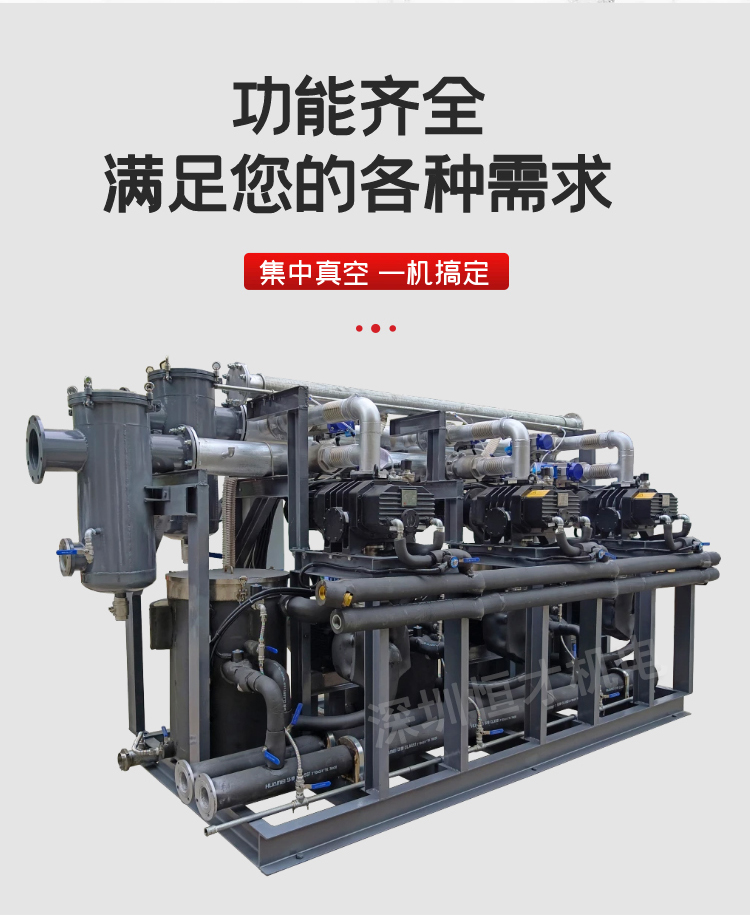
一、傳統(tǒng)泵之殤:塑膠廠的“午夜驚魂”
在一家年產(chǎn)值2億元的家電外殼塑膠廠,傳統(tǒng)旋片泵的“暴雷”時刻堪稱生產(chǎn)部的噩夢:
故障頻發(fā):粉塵與脫模劑混合形成的油泥,每月導致旋片泵卡死3~5次,單次搶修耗時4小時,單日產(chǎn)能損失超15萬元;
真空度跳水:加工冰箱內(nèi)膽吸塑件時,因真空度波動±25%,產(chǎn)品壁厚不均率高達18%,客戶退貨率攀升至行業(yè)均值3倍;
能耗黑洞:為維持真空度,旋片泵需持續(xù)高負荷運轉(zhuǎn),單臺設備年耗電28萬度,電費成本占加工總成本的17%。
更致命的是,傳統(tǒng)泵的“隨機故障”常在深夜爆發(fā)。某次大單交付前夜,因真空泵突然停機,12條生產(chǎn)線被迫停擺,管理層連夜從50公里外調(diào)設備救急,直接損失超80萬元。這類“午夜驚魂”事件,已成為中小塑膠廠的“行業(yè)詛咒”。
二、羅茨水環(huán)機組:破解“不可能三角”的工業(yè)奇跡
羅茨泵與水環(huán)泵的“黃金組合”,通過技術創(chuàng)新實現(xiàn)了“高真空、抗粉塵、低能耗”的完美平衡,其核心突破體現(xiàn)在:
粉塵克星:自清潔密封系統(tǒng)
羅茨泵采用“迷宮密封+氣體吹掃”雙保險設計,轉(zhuǎn)子間隙0.3mm處形成動態(tài)氣簾,可實時吹散直徑0.1mm以上的粉塵顆粒。水環(huán)泵以水為密封介質(zhì),徹底規(guī)避油霧污染。某玩具吸塑廠實測數(shù)據(jù)顯示,改用該機組后,粉塵堆積引發(fā)的故障率從42次/年降至1次/年,設備MTBF(平均無故障時間)從280小時躍升至8760小時。
真空躍遷:三級壓縮技術
羅茨泵負責粗真空階段(大氣壓至1000Pa)的高速抽氣,水環(huán)泵在1000Pa以下接力壓縮,形成“接力式”真空梯度。在汽車儀表盤加工案例中,該機組實現(xiàn):
真空建立速度:0.8秒達成-98kPa,較傳統(tǒng)泵提升300%;
極限真空度:穩(wěn)定在-99.5kPa,使片材拉伸率從180%提升至240%,產(chǎn)品棱角銳度提升40%;
真空度波動:控制在±1.5kPa以內(nèi),徹底消除鼓包、麻點等缺陷。
能耗革命:智能變頻+熱能回收
機組搭載AI變頻算法,可根據(jù)模具真空需求實時調(diào)節(jié)電機轉(zhuǎn)速。某化妝品包裝廠改造后:
單件能耗:從0.28度降至0.11度,年省電費126萬元;
熱能回收:水環(huán)泵循環(huán)水中的余熱被導入模具預熱系統(tǒng),減少天然氣消耗35%;
碳足跡削減:單條生產(chǎn)線年減排CO? 187噸,相當于種植10300棵樹。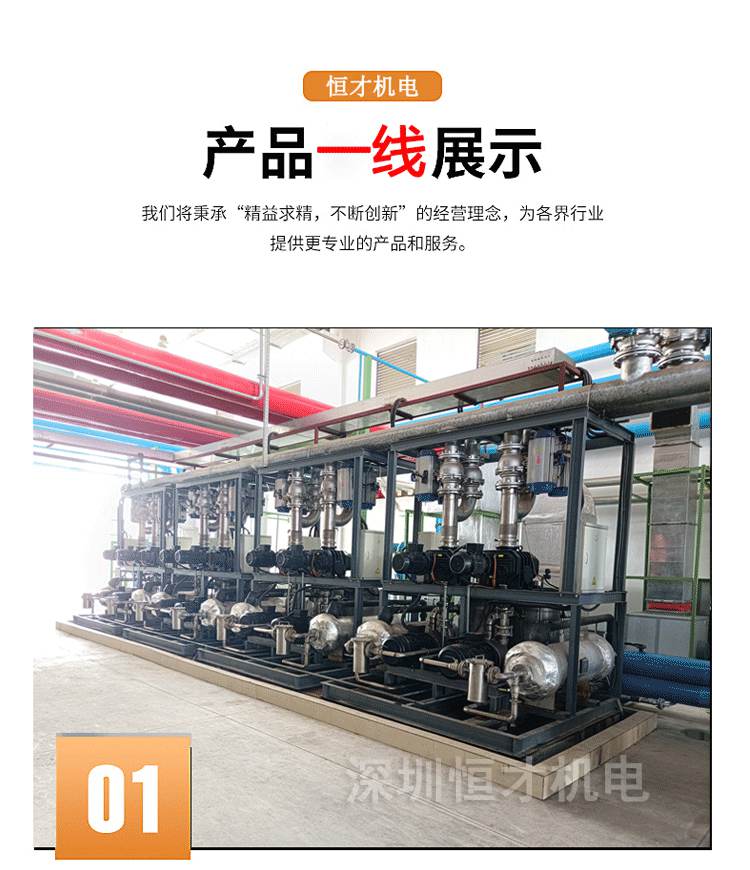
三、實戰(zhàn)革命:從“故障搶修”到“躺贏生產(chǎn)”
某家電巨頭的生產(chǎn)線重生
該企業(yè)原使用12臺2BV水環(huán)泵+旋片泵組合,因粉塵堵塞導致年停機192小時,良品率僅83%。更換羅茨水環(huán)機組后:
醫(yī)療器械包裝廠的“零缺陷”突破
在醫(yī)用透析器外殼吸塑中,傳統(tǒng)泵因真空度不穩(wěn)導致產(chǎn)品壁厚公差±0.15mm,遠超0.05mm的醫(yī)療級標準。改用羅茨水環(huán)機組后:
真空精度:達到±0.02kPa,使產(chǎn)品壁厚公差縮小至±0.03mm;
潔凈度:通過ISO 14644-1 Class 7認證,粉塵殘留量<0.5μg/m3;
認證效率:一次性通過FDA審核,產(chǎn)品溢價能力提升25%。
四、選型與部署:避開“偽節(jié)能”陷阱
科學選型四原則
抽速匹配:按公式Q=K×S×H(Q為抽速,S為模具面積,H為片材厚度,K為1.3~1.5安全系數(shù))選型;
級配優(yōu)化:羅茨泵抽速應為水環(huán)泵的4~6倍,例如500m3/h水環(huán)泵需搭配2000~3000m3/h羅茨泵;
材質(zhì)升級:接觸真空側(cè)部件采用316L不銹鋼,耐腐蝕性提升10倍;
智能擴展:預留物聯(lián)網(wǎng)接口,支持遠程診斷與預測性維護。
部署避坑指南
管路設計:真空管道內(nèi)徑需≥泵口直徑的1.2倍,彎頭數(shù)量≤3個,阻力損失降低40%;
水環(huán)泵溫度控制:循環(huán)水溫度保持在15~25℃,每升高1℃抽速下降2%;
粉塵預處理:在機組前加裝旋風分離器,過濾效率≥99.5%,延長設備壽命3倍。
五、未來圖景:從“設備內(nèi)卷”到“生態(tài)共贏”
隨著工業(yè)4.0的推進,羅茨水環(huán)機組正從“單機神器”進化為“智能生態(tài)節(jié)點”:
數(shù)字孿生系統(tǒng):某頭部企業(yè)已實現(xiàn)真空系統(tǒng)與MES、ERP的深度對接,通過AI算法優(yōu)化排產(chǎn),使設備利用率提升22%;
能源銀行模式:部分廠商推出“真空即服務”(VaaS),企業(yè)按實際抽氣量付費,初期投入降低70%;
循環(huán)經(jīng)濟閉環(huán):水環(huán)泵廢水經(jīng)納米過濾后可循環(huán)使用,配合光伏發(fā)電系統(tǒng),單條生產(chǎn)線年碳收益達58萬元。